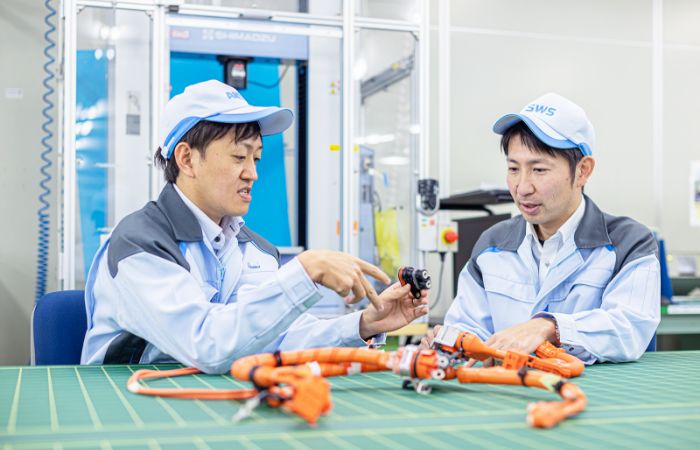
自動車事業プロジェクト
アルミ製ワイヤーハーネスと
高電圧コネクタ
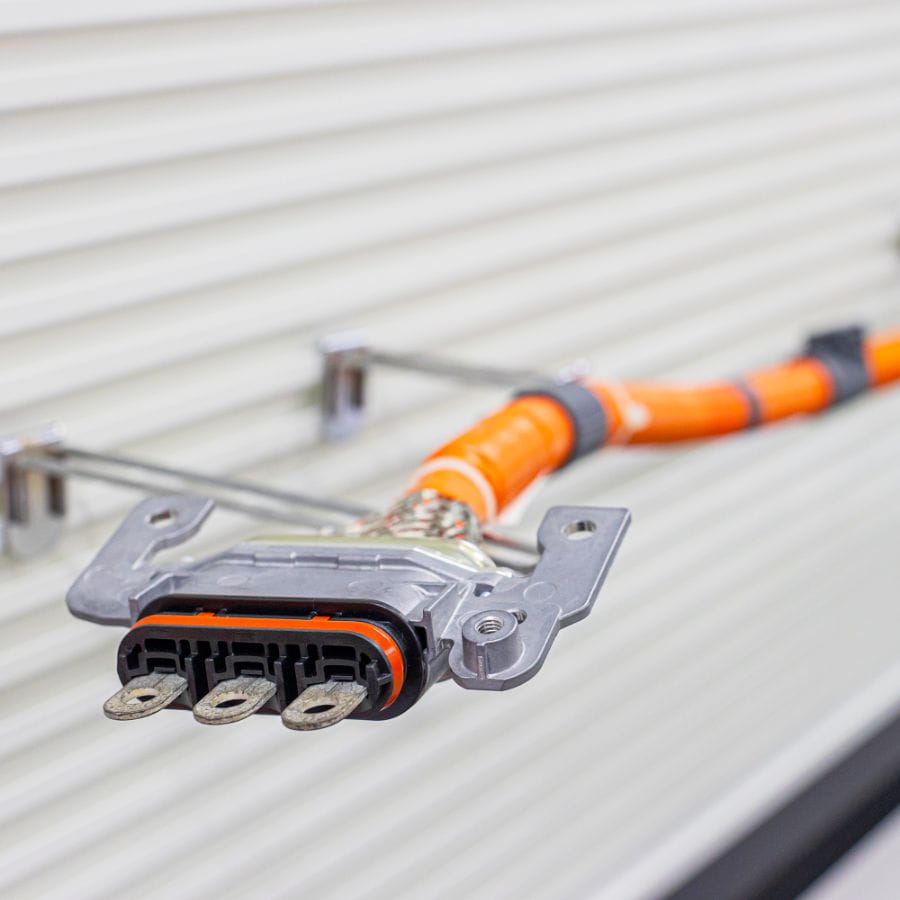
prologue
信頼性は担保しつつ、
新たな技術に挑戦せよ。
自動車業界のグローバル化や、自動車そのもののエレクトロニス化が進展したことで、
ワイヤーハーネスの付加価値は高まり、住友電工グループの屋台骨を支える製品にまで成長した。
しかし、現状維持は衰退の始まりである。時代のニーズにあわせ、ワイヤーハーネスも進化させる必要があった。
-
自動車事業本部
東部営業統轄部小林 諒2011年入社 -
自動車事業本部
東部営業統轄部佐々木 皓2017年入社 -
株式会社オートネットワーク
技術研究所
コネクタ研究部木村 章夫2014年入社 -
住友電装株式会社
ハイブリットモビリティ事業本部黒石 亮2012年入社
※所属部署名等は取材当時のものとなります。
SECTION #01
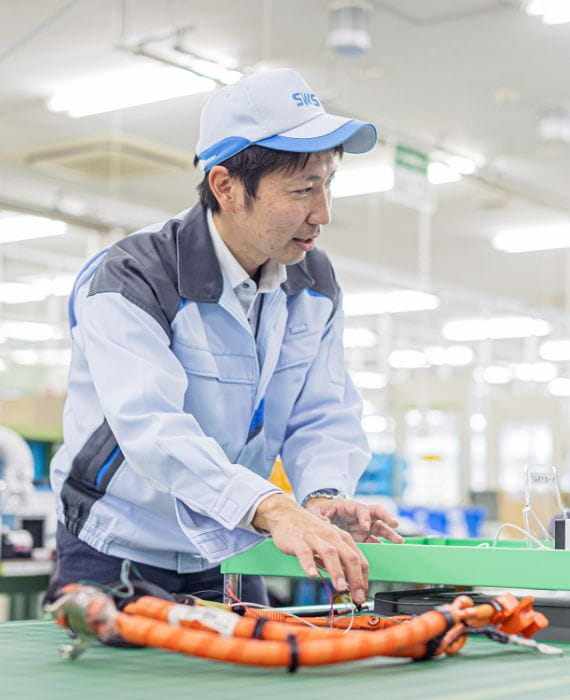
軽量化による燃費の向上
自動車メーカーやその関連製品のメーカーにとって、CO2排出削減は喫緊の課題である。イギリス政府がガソリン車やディーゼル車といった化石燃料自動車の新車販売禁止を2040年から2035年に早める意向を発表するなど、その動きは全世界的に、そして加速度的に進行している。
自動車メーカーにとっての最大の課題は燃費の向上であり、そのためには車体の軽量化が不可欠だった。そこで住友電工グループが取り組みを開始したのが、銅素材で生産されていたワイヤーハーネスをアルミニウムに転換することである。
ワイヤーハーネスとは、電力供給や信号通信に用いられる複数の電線を束にした伝送システムのことである。自動車の車内配線にも多く用いられ、エンジン作動やガソリン燃焼のためのプラグ点火、エアコンやパワーウィンドウ、カーナビなどの製品をつなぎ、エネルギーと情報を伝達する役割を担う。従来型のワイヤーハーネスは銅電線の塊だったため、電線のアルミニウム化は車両の軽量化、ひいては燃費の向上に大きく寄与することが期待された。アルミニウムは非常に軽い素材で、その比重は銅の3分の1程度といわれている。さらに、強度が高く加工性も優れていることから、輸送機器の軽量化に最適な材料のひとつと考えられていたのだ。
自動車メーカーの要請を受け、住友電工グループがアルミ製ワイヤーハーネスの開発に着手したのは2006年のことである。住友電工、住友電装、オートネットワーク技術研究所が三位一体となり、開発に臨んだ。ただ軽くするだけでは意味がない。銅と同等、あるいはそれ以上の信頼性を確保する必要がある。そして、ハイブリッド車や電気自動車の普及が進み、ワイヤーハーネスに対する自動車メーカーの要求レベルも次第に高まっていく中で、技術的なハードルの高い、高圧用アルミハーネスの車両搭載をめざして、社員一人ひとりの想いを一つにした取り組みが行われるようになった。
SECTION #02
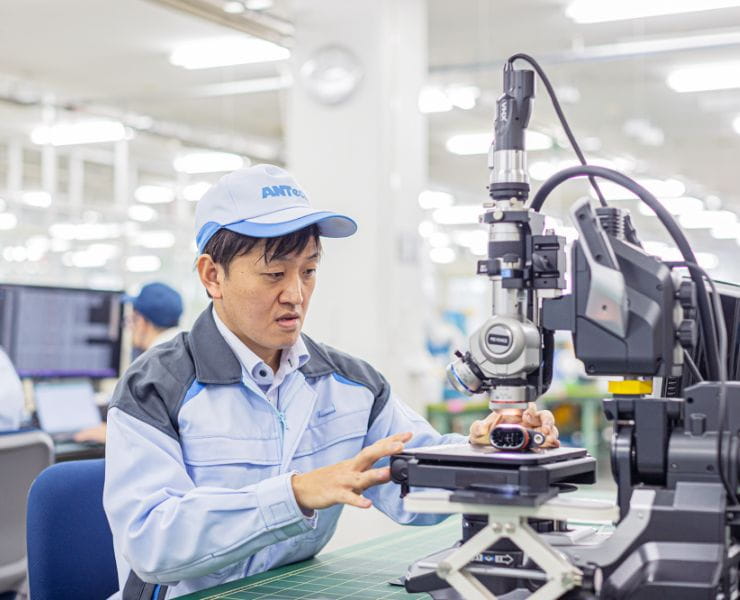
課題を抽出し、実証する
今回のプロジェクトにおいて、住友電工グループが顧客から求められたのは、車内の部品配置を成立させるためのワイヤーハーネスの新たな接続方法とコストダウンである。直近の提案に対する顧客の承認がおりず見送りになり、新たなモデルで雪辱を期すべく、取り組むことになった。
ワイヤーハーネスに使用される電線の本数は、多い車種で約2,000本にもおよぶ。ワイヤーハーネス同士は車内各部各所で接続され、その接続部は圧着と呼ばれる工法で、電線と接続した端子を挿入したコネクタをはめ合わせた構造になっている。
住友電装株式会社でワイヤーハーネス開発の主担当を務める黒石は、一つひとつの課題をつぶしていく作業に腐心した。課題を抽出するだけでもたいへんだが、その課題が問題ないことを証明するために、仮説を立てて評価を実施すること、さらに、それを顧客へ伝え納得してもらうことも、決して一筋縄ではいかない。「難しい内容をいかに簡単にわかりやすく説明するか」を常に意識した。
また、株式会社オートネットワーク技術研究所のコネクタ開発主担当である木村は、製品の特徴や試作品の評価、性能予測に関するエビデンスなど、100ページ以上のPR資料を作成した。顧客への提案・質疑応答は3時間を超え、プレゼン終了時にはすっかり声が枯れてしまったという。
SECTION #03
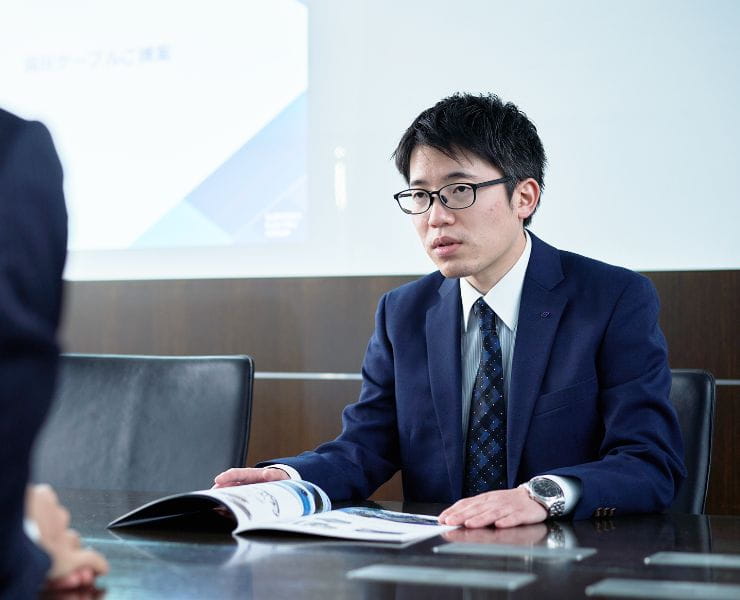
周囲を巻き込み、総力を結集する
黒石や木村が技術的な実証に取り組む一方で、営業担当の佐々木は顧客に対しコスト面の説明を行った。新規技術を含む住友電工グループの製品が、性能のみならずコスト面でも優れていることを、論理的に示さなければならなかった。顧客からは「従来製品から新技術を採用するに当たってのコスト変動の内訳が明確にならない限り、住友電工への発注はない」と明言されていた。つまり、「いくらなのか」だけではなく「なぜそのコストになるのか」を顧客に納得いただくことも重要だということだ。コストの妥当性を示すため、彼は見積基準を再構築することにした。
普段佐々木は東京本社地区所属の営業所で業務を行っていたが、見積基準の再構築にあたっては、技術部門のメンバーのいる三重県鈴鹿市の事業所に毎週のように通い、議論を重ねた。今回のプロジェクトを成功させるためには、住友電工、住友電装、オートネットワーク技術研究所が総力を結集し、営業部門と技術部門が強固に連携することが重要だと、彼は考えていた。営業担当の使命は、顧客からの注文を獲得することだけではない。社内外の意見を調整し、プロジェクトの旗振り役とならなければならないのだ。
新規技術の導入に関して、当初は慎重論も多く聞かれた。というのも、その技術が当該顧客のみならず、ほかのカーメーカーを含めても前例のない、チャレンジングなものだったからだ。挑戦には当然リスクが伴う。受注提案活動の営業主担当である小林は、今後想定される市場規模の拡大を示しつつ、本案件を受注する意義について数字を用いて説明し、社内幹部の説得にあたった。そして最終的には、粘り強い説得の甲斐もあり、無事承認を取りつけたのだった。技術担当や幹部、さらには顧客も巻き込みながらプロジェクトを推進した経験は、若くして責任者を任された彼にとって、大きな成長の機会となった。
SECTION #04
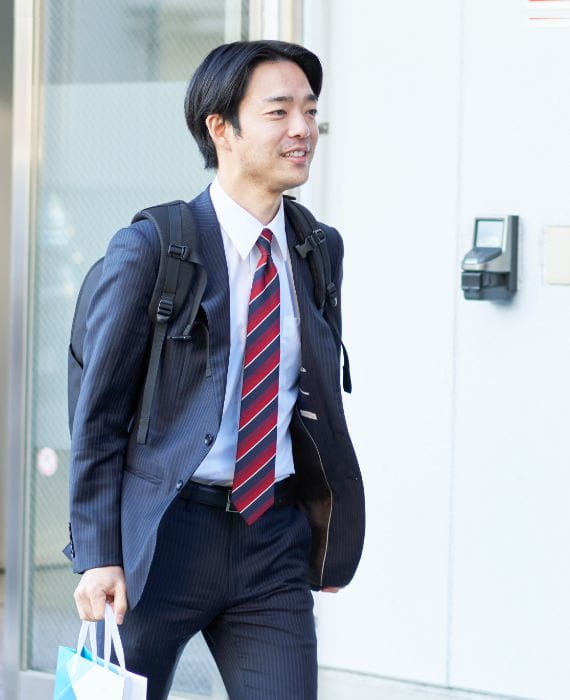
チャレンジングな選択肢
顧客の反応は上々だった。いや、絶賛といってもいい。従来型から変わることのない高い品質を維持しつつ、新しい技術と低コストを両立した製品は、驚きをもって受け入れられた。顧客の技術部門は住友の技術力を知ってくれていたが、異なる視点を持つ購買部門が驚きとともに「お任せしていいですね」と言ってくれたのは印象的であった。
自動車業界は現在、ハイブリッド車や電気自動車に見られる電動化、さらには情報通信技術の進展による知能化、という新たなフェーズを迎えている。新時代が到来すれば、これまでなかったニーズが新たに生まれることになるだろう。未知の領域に足を踏み入れるとき、正解は誰にもわからない。それでも住友電工グループは、知恵を絞り、知恵を寄せ合い、チャレンジングな選択肢を用意する。顧客の期待に応えるだけではなく、顧客の期待を超えていくために。
automotive automotive
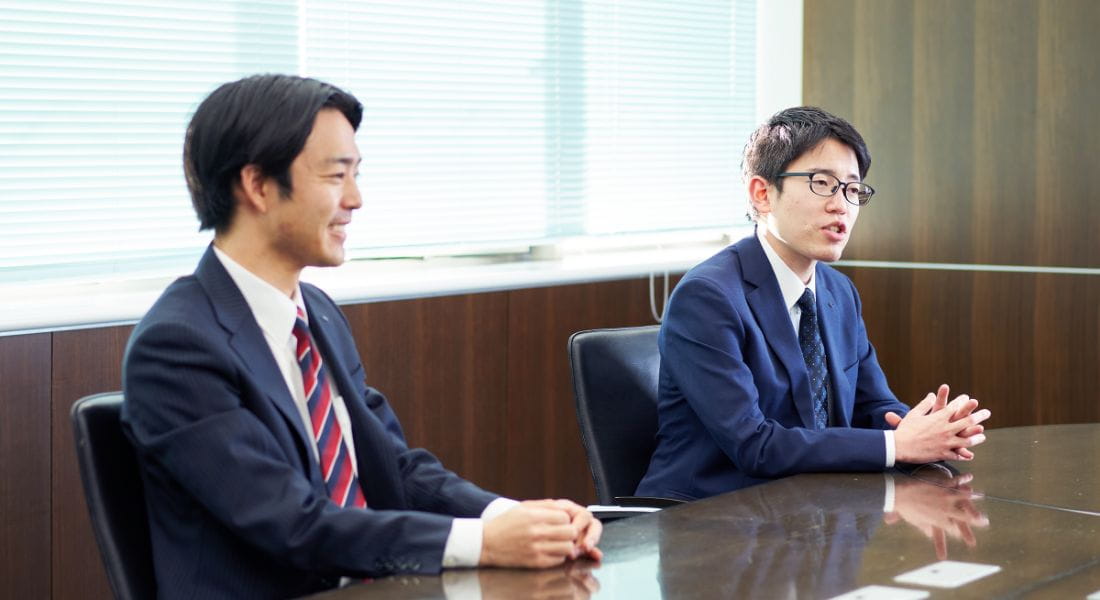