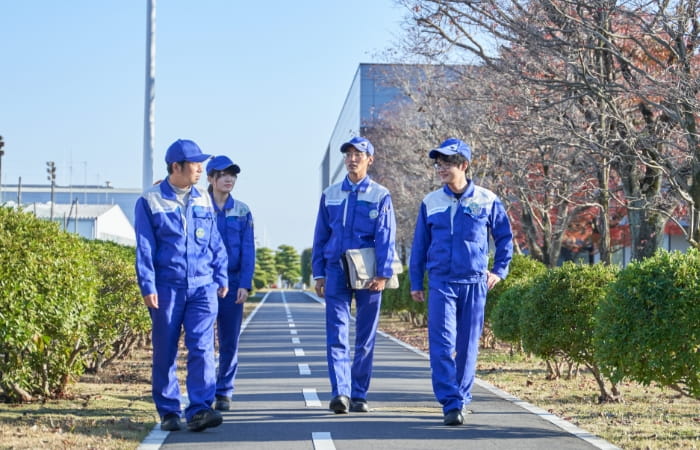
エレクトロニクス事業プロジェクト 車載タブリード
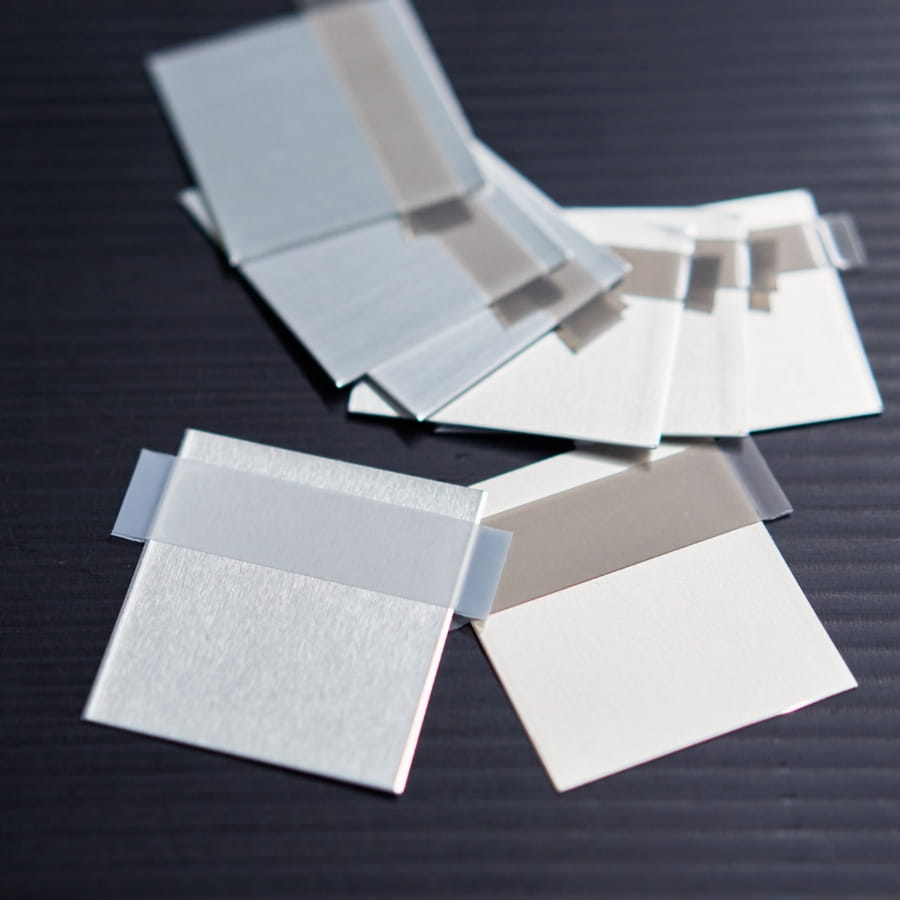
prologue
電池から電気を取り出すリード線が、
電気自動車普及の生命線となる
民生から車載へ活用の場を広げるタブリード。
前例がないなかで量産体制を構築し、今後はリチウムイオン電池から全固体電池への移行に向け、さらなる進化を模索する。
民生用としては20数年、車載用の量産から数えても10年以上になるプロジェクトに迫った。
-
住友電工電子ワイヤー株式会社
コンポーネント製造部 部長宮澤 圭太郎1999年入社 -
住友電工電子ワイヤー株式会社
タブリード部小島 千明2018年入社 -
住友電工電子ワイヤー株式会社
タブリード部伊海 雅和2019年入社 -
住友電工電子ワイヤー株式会社
業務企画部金山 慎介2016年入社
※所属部署名等は取材当時のものとなります。
SECTION #01
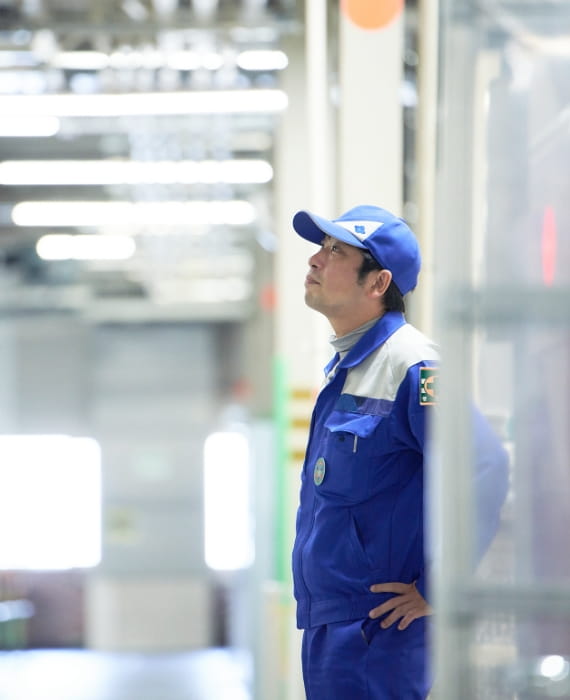
民生から車載、そして量産へ
脱炭素社会の実現に向け、ガソリン車から電気自動車へのシフトが加速している。電気自動車のキーデバイスとなるのは、省スペースでかつ大量の電力を生み出すリチウムイオン電池だ。そして、そのリチウムイオン電池から電気を取り出すリード線が、フラットな導体を絶縁体でラミネートしたタブリードである。
住友電工グループはタブリードのパイオニアとして、1990年代後半から携帯電話などの民生用に供給を開始した。初期段階では導体に表面処理がされていなかったため、絶縁体と導体が接着できず、専門の業者に表面の油や酸化層を除去してもらってから加工するなど、評価サンプルをつくるのにも苦労が多かった。そこで、グループの技術力を結集し、絶縁体と導体の接着の課題を解決。当時の世界最軽量の携帯電話への採用が決まり、その後も安定した品質を守り続けた。
そして、民生用途での安定品質が評価され、より高度な品質・性能が要求される車載案件の引き合いを得るに至る。まずは電動アシスト自転車用電池で引き合いがあり、2002年ごろから車載案件につながりはじめた。しかし、量産にはそれから8年もの期間を要することになった。
1999年に住友電工に入社した宮澤は、設計部門で経験を積み、2009年から工場長として製造の現場に携わった。ときを同じくして、電気自動車に搭載するためのタブリードの量産がはじまる。民生から車載への展開は、世界初の試みだ。前例がないので、評価方法もない。研究段階では問題がなくても量産工程でうまくいかない、といったことは日常茶飯事だった。それでも宮澤は、この車載タブリードプロジェクトを少しずつ軌道に乗せていく。2011年からは、中国の蘇州工場の立ち上げにも尽力。言語や文化、商習慣の異なるローカルスタッフとともに、住友電工のルールで改善を重ね、課題となっていた量産体制を構築した。
SECTION #02
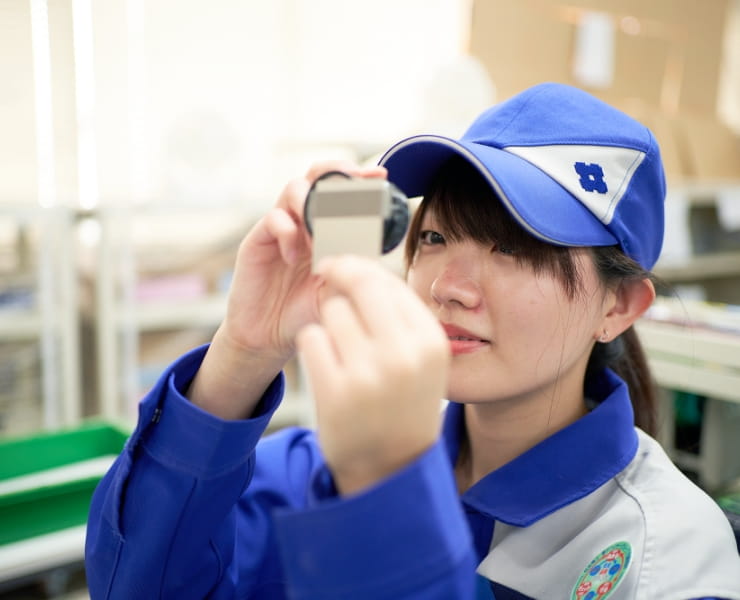
住友電工にしかつくれないものを
入社以来、絶縁体開発に携わってきた小島は、「タブリードは絶縁体と導体しかないシンプルなつくりをしているだけに難しい」と語る。微量の異物を含むだけで品質に大きく影響するため、さまざまなリスクを想定しながら試行錯誤を繰り返す。
住友電工グループの強みとして、絶縁性を保つための独自技術が挙げられる。ひとつが架橋したポリオレフィン樹脂を用いていることで、もうひとつが金属表面の表面処理技術だ。民生用途の際に培った小型化・薄型化・軽量化のための工夫が車載でも活かされている。品質面では、クライアントである自動車メーカーから最高レベルの評価を得ているといっていい。
しかし、求められるのは品質だけではない。価格や生産量、納期の面での要求も厳しい。コストを下げるために材料や配合を見直したり、導体技術による相互性能補填を図ったり、まだまだやれること、やるべきことはあると、小島は考えている。車載タブリードはメーカーのフラッグシップとなる電気自動車に採用されるので、当然失敗は許されない。だからこそ住友電工にしかつくれないものを提供したい、という思いは強い。その限界への挑戦が、彼女のやりがいにつながっている。
SECTION #03
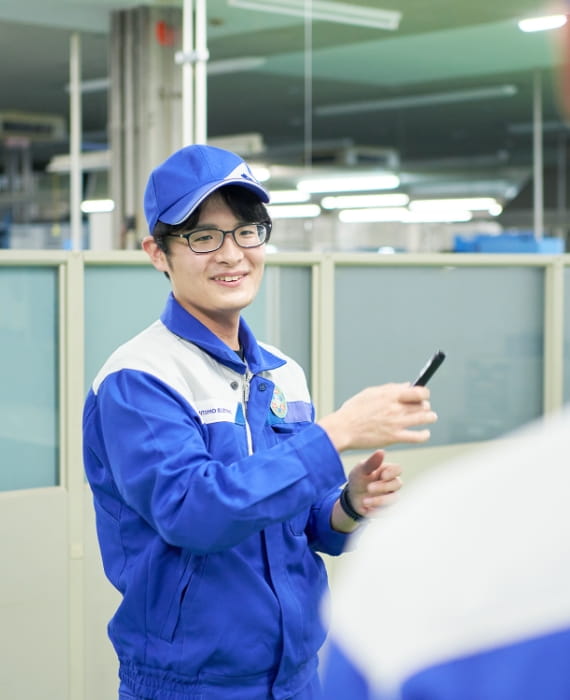
試作を繰り返し、生産量を増やす
2019年入社の伊海は、最初の配属段階から本プロジェクトに関わることになった。ゼロからイチを生み出すのも大変だが、すでに形があるものを市場のニーズにあわせてアップデートしていくのも、また難しいものである。最近は大型で厚型の車載タブリードがひとつのトレンドとなっていて、これまで社内で培われた知見や技術が必ずしも通用するとは限らなかった。
試作品をつくるサイクルは短い。わずか2週間後に、次の試作品の提出を求められることもある。そして、そのサイクルが数ヶ月間にわたって繰り返される。短期間でなんとか結果を出さなければならない。また、上司や先輩から手取り足取り教えられるわけでもないので、自分の頭で考え、自分の意志で動く必要があった。どれだけ厳しい課題でも、絶対にあきらめない。伊海はその一心で自身の業務と向き合う。
一方、業務企画部に籍を置く金山は、車載タブリードの量産化を推進するため、資材の手配や設備の導入など、生産管理の業務を担っている。
タブリードを車載に転用しはじめたころは、一気に市場が拡大すると目されていたが、いざフタを開けてみると、そこまでの伸びはなかった。パウチ型リチウムイオン電池の安全性の検証に想定以上の時間がかったのが、その理由だと考えられている。しかし、実車が街中で走るようになり、信頼性も高まったことで、ようやく市場も成熟してきた。そして今、生産が追いつかないような数量を自動車メーカーから提示されるようになっている。
この課題を解決するのが、金山の使命である。品質を担保しながら生産量を増やすために、彼は部門横断型の業務改善計画の旗振り役となった。100個生産しようと思って設備投資したのに、実際は80個しか生産できなかった、ということもある。机上の計算だけでは、事業は成り立たないのだ。そこで彼は、各部門で業務の見える化を行い、そのデータをもとに工場で働く社員たちと地道に意見交換を行った。部門ごとに仕事の進め方やモノづくりに対する考え方が微妙に違うため、さまざまな観点から情報を収集し、それを整理したうえで関係者全員に納得してもらう必要があった。
SECTION #04

次世代の全固体電池への移行に向けて
現在住友電工では、リチウムイオン電池から次世代型の全固体電池への移行に向け、自動車メーカーと直接コミュケーションをとりながら開発を進めている。
リチウムイオン電池は、リチウムイオンが液体の電解質の中で正極と負極との間を行き来し、その動きで充電・放電する仕組みだ。一方、全固体電池は電解質が固体になり、電解液では使えなかった電極材を使えるようになる。その結果、充電できるエネルギー密度が上がり、航続距離が延びるのだ。
これまで同社は独自の技術や一貫生産体制を強みに、高品質の車載タブリードを市場に供給してきた。ただ、10年以上にわたって競争優位性を築いてきた製品にとらわれすぎると、今後の進化は望めない。だからこそ宮澤は、若手エンジニアたちの可能性や情熱に大きな期待を寄せる。
小島は「やっぱり住友電工のタブリードじゃないとダメだよね」と言われる製品開発に力を注ぎ、伊海は生産技術分野の知見を広げつつ、将来的な海外駐在も視野に入れる。今後、電気自動車の台数は指数関数的に増えていくだろう。市場の伸びに追従できるよう、金山は本プロジェクトをさらに強化することを誓う。
電気自動車の普及には新たな形の電池が必要不可欠であり、電池から電気を取り出すリード線であるタブリードが、まさにその生命線となるだろう。
Electronics business
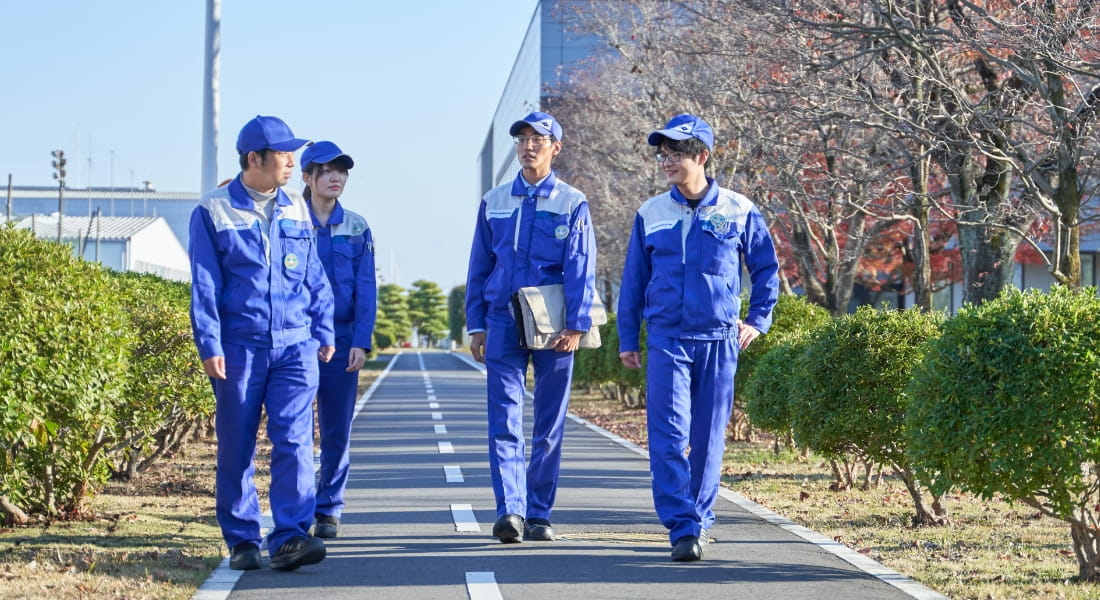