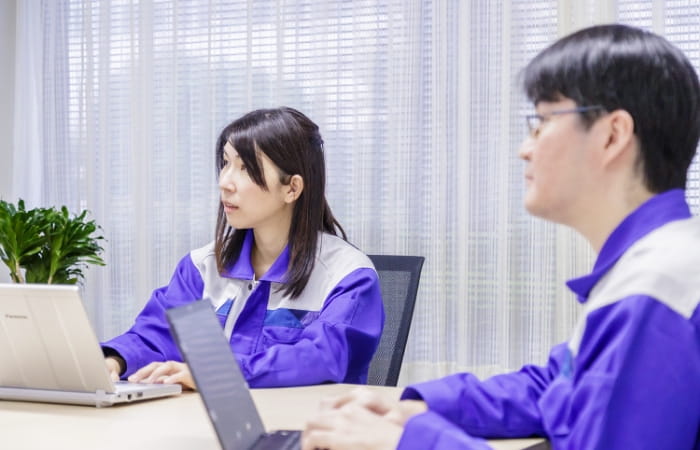
産業素材事業プロジェクト
バインダレス
CBN工具の開発
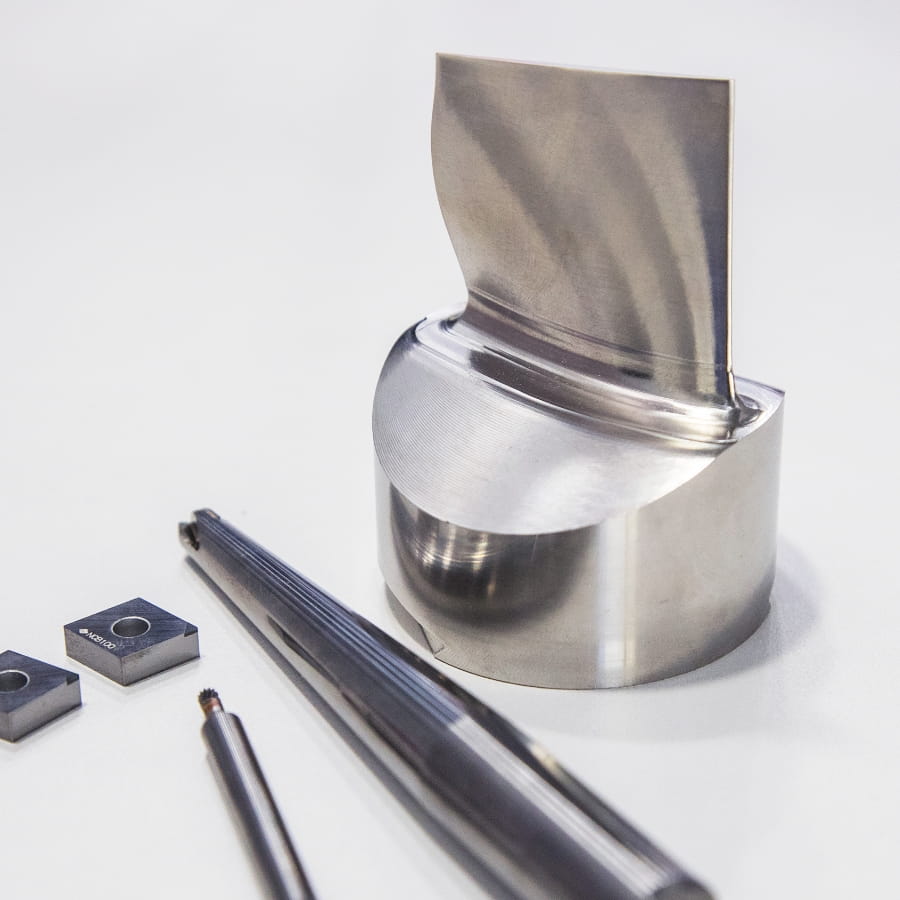
prologue
高硬度のバインダレスCBN工具が
新たな市場を生み出す
バインダレスCBN自体は以前から存在していたが、切削工具としての製品化には結びついていなかった。研究開発部門から材料開発部門へ、さらに加工製造部門、製品開発部門、営業部門へとバトンをつなぎ、顧客の新たなニーズを掘り起こしていく。
-
住友電工ハードメタル株式会社
ダイヤ・CBN開発部阿部 真知子2007年入社 -
住友電工ハードメタル株式会社
ダイヤ・CBN開発部石田 雄2010年入社 -
住友電工ハードメタル株式会社
ダイヤ・CBN開発部東 泰助2010年入社 -
SUMITOMO ELECTRIC
HARTMETALL GmbH.(ドイツ)松田 裕介2008年入社
※所属部署名等は取材当時のものとなります。
SECTION #01
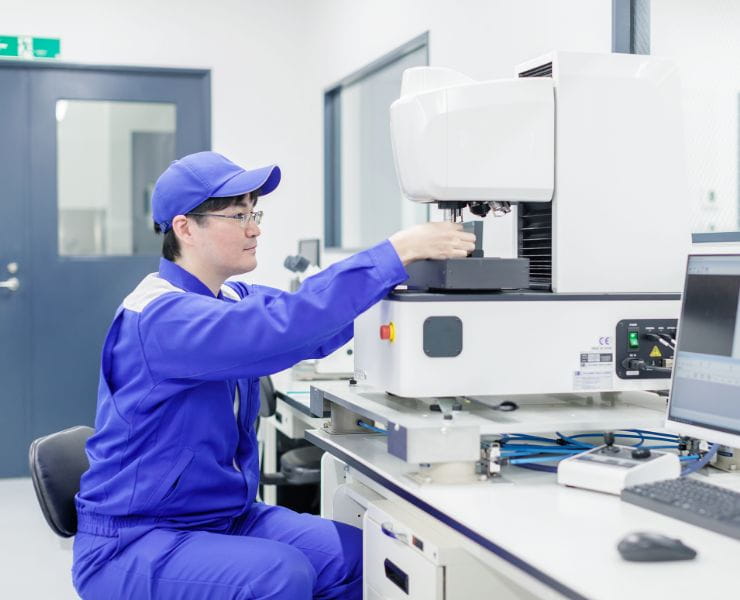
まともな焼結体が得られない
バインダレスCBN工具の開発プロジェクトは、2010年10月に立ち上がった。CBNは立体晶窒化ホウ素焼結体のことで、ダイヤモンドに次ぐ硬度と耐鉄反応性に優れることを特徴とする 工具材料である。主に自動車産業での焼入鋼、鋳鉄や焼結合金の高速仕上げ加工で用いられている。
バインダー(結合剤)を一切含まないバインダレスCBN自体を作製する技術は1990年代から存在していたが、実用化には至っていなかった。本プロジェクトでは、ナノ多結晶ダイヤモンドの技術を用いたCBNの新製品開発が検討されることに。実用化となれば、これまで削れなかった素材の加工が可能となり、新たな市場の開拓が期待できた。
素材開発の主担当は、当時アドバンストマテリアル研究所に在籍していた、入社1年目の石田である。プロジェクト開始から半年間は、まともな焼結体が一切得られなかった。とにかく硬い素材だったため、まっぷたつに割れたり、どこかしらに亀裂が入ったりしたのだ。そこで彼は、欠片を使って評価を進めることにする。上司や先輩社員に協力を仰ぎながら、製造時の問題を洗い出し、それらをひとつずつ解決していった。
また、バインダレスCBNは従来のCBNに比べて体積が小さくコストが高い、という問題が別にあった。それについても試行錯誤を繰り返し、当初の10倍のサイズの焼結体を得ることに成功する。そして、どうにか販売可能なレベルまでコストを抑えられる目途がたったところで、プロジェクトは住友電工ハードメタル株式会社のダイヤ・CBN開発部に移管された。
SECTION #02

流れをつくり、流れを決める
石田が開発した素材を量産化する仕組みをつくったのが阿部である。安定製造が可能な条件を整理し、さらに品質保証の観点から、製造上の異常を見つけ出す方法を検証しなければならなかった。従来のCBN素材製造における検査方法や、トラブルシューティングの常識はまったく通用しない。すべてがゼロベースでの構築となった。
素材の中に異常があるかどうかは、精密な検査をすれば判明する。しかし、量産においては検査費も製造コストに含まれるため、毎回実施するわけにはいかない。阿部は精密検査と簡易検査の相関関係を一つひとつ確認しながら、品質とコストを両立させていった。
彼女は以前、バインダレスダイヤモンド素材を切削工具用途に適用し製品化する、という画期的な取り組みに携わった経験がある。バインダレスダイヤモンドはバインダレスCBN以上に硬いため、加工が難しい。ゼロから加工方法を立上げ、工具の量産化に漕ぎ着けた経験を活かし、今回も石田から受け取ったバトンを、いい形で次につなげたかった。
研究開発部門で生み出したバインダレスCBNという素材を、材料開発部門が受け取って量産化する。そして、その素材を使って工具をつくる過程では加工製造部門が、顧客の要求を満たす製品にする過程では製品開発部門が、市場に投入する過程では営業部門が、といった具合に、全社横断的な連携が求められた。
上流工程に位置する阿部は、同じ製造条件でも多少の差異が発生するなかで、「バインダレスCBNの素材はこういうものだ」という定義づけを行う必要がある。自身が見逃した不具合は、最悪の場合、顧客のところまで流れて行ってしまう。それだけにプレッシャーは大きかった。
SECTION #03
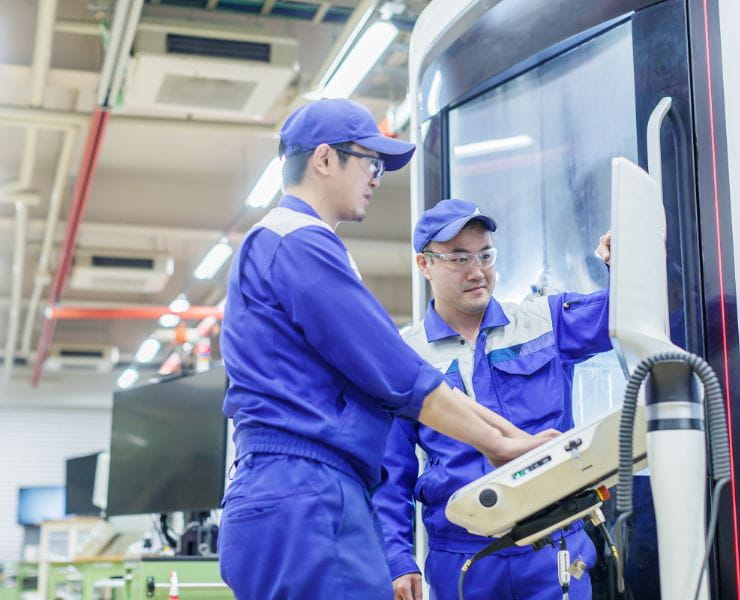
新たな成長産業での市場拡大を狙う
前述の通り、バインダレスCBN自体は以前から存在していたが、切削工具としての製品化には結びついていなかった。先人がつくりあげた素晴らしい独自素材を、どのように発展させて市場に送り込むのか。さらに、どうやって顧客に売り込んでいくのか。それを考えるのが東の役目だった。彼は製品開発主管グループの担当として、国内外問わず直接顧客に訪問し、顧客の困りごと、ニーズを直に感じ取り、設計に落とし込みながら工具の試作および社内評価を繰り返し実施した。高硬度な材料故の加工のし難さから、狙いの工具形状にならない、加工コストが大幅に上がる等の課題に直面したが、上司、同僚の他、生産技術部門、製造部門、営業部門など多数の関係者にも協力を仰ぎ、早期市場投入に向けて邁進し、実用レベルまで漕ぎつけた。
世界でまだない新たな価値を生み出す工具開発、高硬度のバインダレスCBN材料を工具形状に加工する最先端の生産技術開発、、、なにか新しいものを生み出そうとするとき、正解は誰にもわからない。必死で考え、やるべきことを決めたら、あとは前進あるのみ。それが東のポリシーだった。
住友電工にしかない製品によって課題解決できる可能性があることをPRできれば、これまでほとんど接点のなかった顧客からも声をかけられる。さらに同社の技術力に対する理解が深まることによって、バインダレスCBN工具以外の製品への波及効果が生まれるとの確信があった。切削工具メーカーが集まる工業会において2020年度の技術功績大賞を受賞した実績が、そのことを如実に物語っている。
また、自動車の電動化など100年に一度の産業変革が起こるなか、グローバル競争力を高めるためには、新たな成長産業での市場拡大が重要かつ喫緊の課題である。今回のバインダレスCBN工具の実用化は、同社にとっては馴染みの薄い航空機産業や医療産業にも食い込んでいける可能性を示したのだった。
SECTION #04
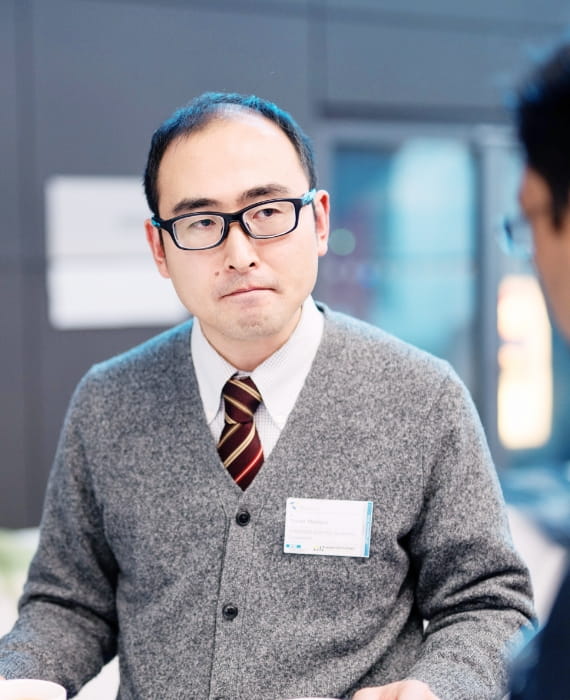
実を結ぶ瞬間、そして次の挑戦へ
最後にバトンを引き継ぐのは、顧客と直接接する松田である。彼は9年間のCBN工具開発時代を経て、現在はドイツの工具開発部でマネージャーを務めている。石田、阿部、東らが開発した工具を顧客に紹介し、販売に結び付けるのが彼の役割だ。
赴任した2017年、住友電工は航空機産業や医療産業ではシェアが高くなく、せっかくの良い工具もすぐに評価するのが難しかった。しかし100社以上の企業が参加するイギリス・シェフィールド大学主催の航空機コンソーシアム「AMRC (Advanced Manufacturing Research Centre)」に参画したことで、航空機産業の顧客との接点が広がった。AMRCでのバインダレスCBN工具の評価プロジェクトの成功をきっかけに、参加企業に対して積極的にPRを行い、新たなコネクションを築いていった。実際に製品を使用した顧客で狙い通りの好結果が出ると、「Excellent(エクセレント)!」や「Wunderbar(ヴンダバー)!」(前者が英語、後者がドイツ語で、いずれも「素晴らしい」の意)などの声があがった。
バインダレスCBN工具は、航空機部品に使用される難削材のインコネルやチタンだけでなく、人工関節に使用されるコバルトクロムでも抜群の性能を発揮し、顧客との新たな関係を構築することに成功した。工具の性能について信頼を得たことで、他の工具の評価にも展開することができた。さらに、良好な関係が構築できた顧客からは、次世代難削材の加工プロジェクトについても相談を受けるようになった。より削り難い素材を加工するための、より高性能な工具の開発。住友電工の挑戦はまだまだ続く。
Industrial Materials
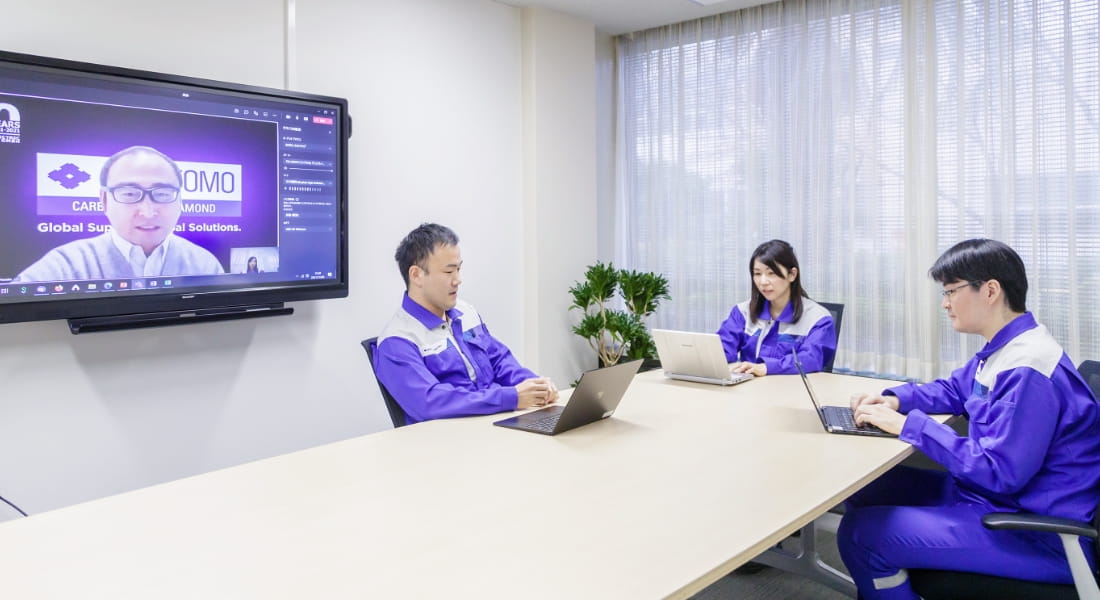